Innovations & Potentials in Mining Equipment
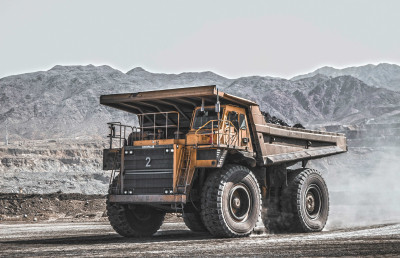
The rising demand for raw materials is fueling increased investments in new mines and mining equipment. At the same time, mining companies are intensifying efforts to boost productivity and reduce costs. Electrification is becoming a key priority to eliminate underground emissions and lower fuel expenses, while automation in mining is advancing faster than in other sectors. For component suppliers, this presents above-average growth potential and the opportunity to position high-tech solutions in a highly innovative market.
Our calculations indicate that approximately 40,000 mining machines—including haul trucks, excavators, wheel loaders, drilling rigs, crushers, and screening plants—were produced in 2023. The rising demand for raw materials, driven by population growth, urbanization, and the shift towards e-mobility and renewable energy, is fueling investments in new mines and mining equipment. Depending on the scenario, we anticipate a compound average growth rate of 4–6% in this sector through 2030.
Emerging markets and resource-rich regions are expected to deliver the highest growth rates. Africa is seeing increasing mining investments (e.g., cobalt in the Democratic Republic of Congo, iron ore in West Africa). South America—particularly Brazil, Chile, and Peru—is investing heavily in mining projects (copper, lithium). Australia and China are also home to large-scale mining projects. Meanwhile, North American mining companies are modernizing their truck fleets with autonomous technology.
Like construction machines and agricultural machines, mining equipment is undergoing significant technological transformations, driven by electrification, automation, and digitalization.
Mining haul trucks and loaders: Electrification is gaining momentum, primarily driven by the goal of eliminating diesel emissions in underground operations and reducing fuel costs. Battery-electric underground loaders and haul trucks (LHDs) are already in use, eliminating exhaust emissions and reducing the need for expensive ventilation. In surface mining, companies are experimenting with hybrid and hydrogen-powered haul trucks. Trolley-assist trucks, which use overhead power lines, are also employed in large open-pit mines. Beyond emissions reduction, electric drivetrains offer productivity advantages due to high torque and efficiency.
Electrification increases demands on component suppliers, particularly in battery and charging technology, electric motors, power electronics, and thermal management.
Automation is most advanced in mining. Over 2,000 autonomous haul trucks are currently in operation or autonomy-ready worldwide. Major mining companies such as BHP and Rio Tinto operate entire fleets of driverless trucks in Australian open-pit mines, controlled by centralized systems. These autonomous trucks follow precise routes, stop for obstacles, and optimize load distribution—resulting in higher productivity, fewer accidents, and extended equipment lifespan. Caterpillar and Komatsu dominate this market, with their Autonomous Haulage Systems accounting for approximately 74% of all autonomous haul trucks.
Beyond haul trucks, drilling rigs are also being automated. Automated drilling rigs can independently position and drill holes (critical for blast operations in open-pit mining). Some mines already use remotely controlled or autonomous drills, improving safety by removing personnel from hazardous areas. Underground operations are increasingly employing teleoperated or semi-autonomous loaders and shuttle vehicles, controlled remotely for safer operations. Overall, autonomous technology in mining is considered mature and economically advantageous, accelerating its adoption.
Mining equipment such as haul trucks and drills showcase the potential of autonomous technology (24/7 operation without fatigue, minimal downtime) and often serve as technology drivers for other industries. The insights gained from these systems contribute to the development of autonomous trucks and construction machinery. For component suppliers, the automation trend increases the importance of sensor technology, control systems, and software solutions.
Alongside physical automation, the digitalization of mining equipment and workflows is accelerating. Modern mining machines are equipped with sensors and communication technology, generating vast amounts of data. The analysis of this data enables greater efficiency, predictive maintenance, and improved decision-making, leading to direct financial benefits.
Digital Mines: All machines—from drilling rigs to haul trucks and crushers—are monitored and coordinated in real time. Telematics systems transmit operational data (position, fuel consumption, temperature, utilization) to control centers. AI-driven analytics can predict maintenance needs (predictive maintenance) and optimize processes.
Example: Sensors in crushers and screening plants measure vibrations and loads; software automatically adjusts the feed rate to maintain optimal throughput and prevent breakdowns. Mining operators are investing heavily in IT systems, connectivity, and analytical software to maximize output from existing equipment before making new capital investments.
For component suppliers—whether manufacturers of engines, hydraulics, sensors, or software—these technological shifts present attractive opportunities. However, mining machinery often imposes more extreme demands on components than construction and agricultural equipment.
Diesel engines have traditionally dominated off-highway machinery. Future drivetrains must be cleaner and more efficient. Engine manufacturers must provide emissions control technologies (e.g., particulate filters, SCR catalysts) to meet increasingly stringent regulations such as EU Stage V and US Tier 4 Final. In mining, where many vehicles operate on private sites without direct emissions regulations, the pressure to reduce emissions stems primarily from corporate ESG goals. Electrification introduces new challenges: Suppliers of battery systems, electric motors, and power electronics are becoming critical partners. Open-pit haul trucks, for example, require megawatt-scale electric drives and robust battery or hydrogen fuel cell systems—technically demanding solutions that create niche opportunities for specialized suppliers.
Hydraulic systems are the backbone of power transmission in excavators, wheel loaders, drilling rigs, and tractors (lifting mechanisms, steering). In mining, hydraulic cylinders and pumps must withstand extreme loads and continuous operation. For example, hydraulic excavators with bucket capacities of over 40 m³, used to load earth into dump trucks, operate in three-shift cycles, demanding the highest levels of reliability. Suppliers of hydraulic components must provide materials and seals that are abrasion-resistant and temperature-stable.
Opportunity for Innovation: The integration of hydraulics with electronics (electrohydraulic control) enables more precise control and energy savings. Intelligent valves can regulate flow volume as needed, reducing energy loss through heat dissipation. Suppliers offering such advanced hydraulic solutions will be in high demand across all sectors—for example, in excavators with automated bucket control.
Software solutions are increasingly becoming a key part of machinery offerings. While OEMs usually equip their machines with proprietary software, they also rely on external software partners for fleet management, autonomy, and predictive maintenance. This opens opportunities for IT companies and specialized providers to introduce their algorithms and platforms into the off-highway sector.
In mining, software solutions for mine planning and optimization are often integrated from third-party providers. Companies like Caterpillar and Komatsu invest in mining automation startups and collaborate directly with mining firms to bring autonomous systems to market. AI-powered services—such as image recognition for ground conditions or route optimization—can also be offered as supplier add-ons.
For traditional component suppliers (e.g., hydraulic manufacturers), this shift creates the need to open system interfaces or develop in-house software expertise to remain competitive in the digital ecosystem. A sensor supplier, for example, can differentiate itself by offering an integrated data analysis tool.
Overall, a portion of the value chain is shifting toward software and data. Suppliers should embrace this trend, whether through partnerships with IT firms or by establishing dedicated digital divisions.
The increasing automation and digitalization of machinery make sensors, control units, and communication modules indispensable. Mining equipment, for instance, requires radar, LiDAR, and camera systems for autonomous operation. An autonomous dump truck is equipped with multiple radar units and laser scanners to detect obstacles. Suppliers that can provide rugged sensors for dusty and high-vibration environments will find a strong market niche.
High-precision position sensors (GNSS/GPS) are particularly critical in mining—ensuring location accuracy within 10 cm for dump truck routes. Electronic control units (ECUs) coordinate these sensors and actuators, with their complexity and number increasing in all types of machinery.
For suppliers of electronic components, this trend translates into growing sales but also a need for software expertise. Many OEMs require that sensors and control units be software-integrated and update-capable. Additionally, telematics modules (GPS + cellular communication) are in high demand. Many manufacturers source these from third-party providers, creating a market for standardized, fail-safe telematics boxes. Component suppliers specializing in electronics and sensors for harsh environments play a key role in automation and digitalization and are essential partners for OEMs.
In summary, component suppliers must adapt their offerings to meet these new demands—focusing on higher power density in drivetrains, robustness in mechanics and sensors, and intelligence in electronics and software.
The importance of efficient electric motors, high-performance batteries, precise sensor technology, and smart controls is growing. Suppliers that introduce innovative solutions early—such as new sensor systems for autonomous functions or ultra-durable hydraulic valves—can establish themselves in this expanding market. Given their scale and operational intensity, mining machines (haul trucks, excavators, loaders, drills, crushers, and screens) impose the highest technical requirements, often translating into higher margins and long-term supply contracts.
Our Mobile Working Machines Worldwide Database contains detailed information about all relevant manufacturers of mining equipment.